What Is a Pneumatic Filter?
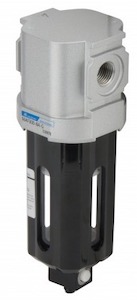
Figure 1: A pneumatic filter
When generating compressed air, contaminants such as moisture and oil enter the system. Without a pneumatic filter, industries that require a high degree of sanitation, like industrial food producers, risk having excess contaminants in their process. This article looks at pneumatic filters, how they work, and how pneumatic applications use pneumatic filters to keep compressed air clean.
Table of contents
- Pneumatic filter design and operation
- Pneumatic filter installation and maintenance
- Removing water from a compressed air system
- FAQs
View our online selection of filters, regulators & lubricators!
Pneumatic filter design and operation
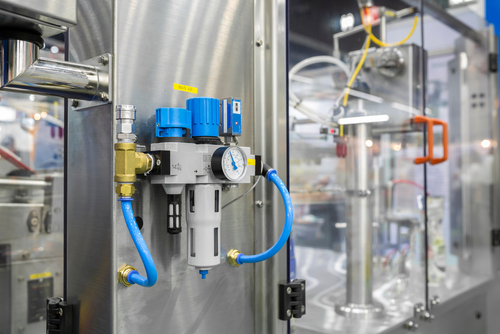
Figure 2: A pneumatic filter
Pneumatic filters can be singular units or part of a more complex unit, such as a filter, regulator, lubricator (FRL) unit. A filter’s rating depends on the size of particles it can trap. Filters that can trap particles ranging from 40 - 60 microns are suitable for most industrial applications. Filters that trap particles ranging from 5 - 25 microns are commonly available. Note that the finer the filter component, the larger the pressure drop across the air filter.
The specifications of pneumatic filters vary among manufacturers, but the following pneumatic filter elements are typical:
- Body: Air filter bodies can be aluminum, PA 66, Zinc die-cast, and stainless steel. This variety allows pneumatic air filters to operate in a broader range of applications. See our chemical resistance guide to learn more.
- Bowl: Condensate from the air collects in the bowl. Typically bowls are polycarbonate. However, stainless steel bowls are available for pressures above 10.5 bar (152 psi) or temperatures above 50 °C (122 °F).
- Whirl disc: Compressed air entering the filter’s bowl first hits the whirl disc. This disc causes the air to move in a circular motion. This motion creates a centrifugal force that separates condensate from the compressed air. The condensate gathers on the bottom of the bowl.
- Baffle plate: A baffle plate at the bottom of the filter element creates a quiet zone at the bottom of the bowl. This prevents circulating air from picking up the condensate that gathers on the bowl’s bottom.
-
Filter element: The filter element removes particles and oil from the compressed air. Typical filter elements in pneumatic filters are sintered bronze and resin paper.
- Sintered bronze: Sintering means using high temperature and pressure to combine powdered material into a single mass. This is done without bringing the material to its melting point. When creating a filter, the resulting bronze filter is porous and uncleanable.
- Resin paper: Resin-saturated paper captures solid particles as compressed air passes through the filter. These filters are cleanable by brushing them or flowing through the filter in the reverse direction.
- Conical cover: The conical cover around the entrance to the filter element stops air from flowing directly through the pneumatic filter without condensate and large particles first dropping out.
Read our pneumatic tool oil article to learn more about the various oil types used in air tools.
Pneumatic filter installation and maintenance
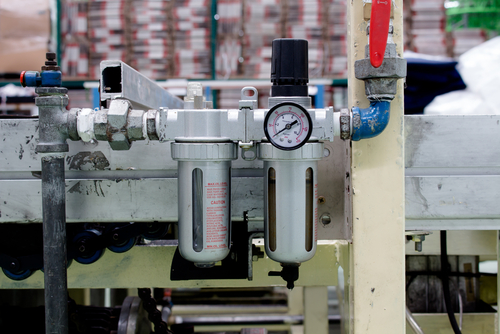
Figure 3: A pneumatic filter installed in a system
Installing an inline pneumatic filter is straightforward. It can go anywhere upstream of a component that cannot handle excess moisture or too large particles. Install a pneumatic filter as a singular unit or connected to a regulator, lubricator, or both. When installing, the air filter’s bowl must be facing downward.
Pneumatic filter maintenance can be minimal if an air dryer connects to the discharge of the air compressor. An air dryer quickly cools compressed air to condense the moisture into larger drops. A typical dryer has desiccating material to trap the condensed moisture. The dryer then quickly heats what remains to return it to compressed air.
Regular air filter maintenance involves draining the bowl and replacing or removing the filter element.
- Draining the bowl: The bottom of the pneumatic filter’s bowl has a removable stopper for draining the collected moisture. Most air filters have a transparent section of the bowl so a user can determine how much moisture has collected on the bottom.
- Replacing or cleaning the filter: A porous filter, such as a sintered bronze filter, requires replacement because it will eventually clog. It is possible to clean a paper filter saturated with resin.
Removing water from a compressed air system
Water can significantly damage air tools and contaminate processes that use compressed air. It may cause paint to peel, mold to grow inside the equipment, and raise the humidity levels of the final product, all of which make the resulting work very poor or unsafe.
The process of water removal follows a series of steps. Several pneumatic filters in series can remove moisture at various stages of compression and delivery. Most systems have a filter just after the air is cooled below ambient temperatures. This catches about 70% of the moisture in the compressed air when it is in liquid form. This enables the devices to collect solid particulates, such as dust and pollen, that may be stuck in the water.
A pre-filter removes water and solids up to three microns. It is the initial and mandatory filter for all pneumatic equipment. In addition, the use of the filter enables the organization to achieve theISO 8573-1 Class 3 air quality standard. Downstream filters further capture the particles and moisture remaining after the initial one.
Removing oil from a compressed air system
Oil is as destructive as moisture in pneumatic systems. Adding oil to various parts for lubrication ends in some oil releasing into the ambient air. In some applications, oil can become a residue on the final product, causing the breakdown of the component material or sticking to components or parts of the system.
Oil removal from compressed air is also accomplished in stages, with various filters removing oil particles from the compression and air delivery systems. Pre-filters can remove a high amount of oil in the initial stage, while an adsorbing pneumatic oil filter removes the rest.
Pneumatic coalescing filters
Pneumatic coalescing filters remove oils and air vapor as the air gets to the system. However, they can also be used on condensed air later in the system. Pneumatic coalescing filters can remove particles as small as 0.3 to 0.6 microns. They achieve this by using a coarse mat with very fine fibers that are small enough to pick up fine particles. The particles channel to a quiet zone and drain manually or automatically.
Air enters from the left to the liquid separator, where a bowl has a filter element. The element removes the particles from the air before it moves out the other end. These oil and water particles then collect just behind the baffle for draining. The baffler restrains fluid and directs it along a specific path.
FAQs
Can you wash pneumatic filter elements?
This depends on the type of pneumatic filter. Washing filter components makes them less efficient in removing particles. In industrial applications, new ones replace these elements for efficiency.
Manual or automatic drainage systems?
Manual systems are ideal for smaller pneumatic systems with a low volume of air used. Automatic drainage systems are vital in industrial applications.
Can you achieve 100% air purity?
Some particles in the air are too small to be filtered out. However, most pneumatic air filter systems achieve over 99.8% air purity through a system of primary and secondary devices.