Direct Acting Solenoid Valve
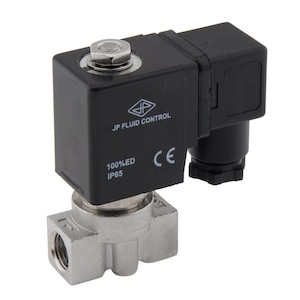
Figure 1: Direct acting solenoid valve
Solenoid valves are widely used in various industries for controlling the flow of liquids and gasses. A direct acting solenoid valve uses the electromagnetic force generated by the energized coil to control the flow of liquid or gas. This article explores the features, construction, advantages and disadvantages of direct acting solenoid valves, along with a comparison with other valve types, including:
Read our overview article on solenoid valves for the construction, working, and applications of solenoid valves.
Table of contents
View our online selection of solenoid valves!
Working principle
In a normally closed direct acting solenoid valve, the spring (Figure 2 labeled D) exerts a force on the plunger (Figure 2 labeled E), forcing it to block the orifice with the seal (Figure 2 labeled F). When power is applied to the coil (Figure 2 labeled A), it creates an electromagnetic field. This causes the plunger to move up, overcoming the spring force, thus opening the orifice and allowing the media to pass through. A normally open valve has the same components but works in the opposite way.
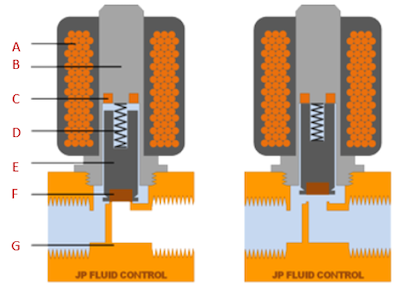
Figure 2: Direct acting solenoid valve working principle and components: coil (A), armature (B), shading ring (C), spring (D), plunger (E), seal (F), and valve body (G). This figure shows the valve in the closed (left) and open (right) states.
Advantages
- No minimum operating pressure: Direct-operated solenoid valves require no minimum operating pressure or pressure difference to be used from 0 bar up to the maximum allowable pressure. They can be used in negative-pressure circuits too.
- Fast startup: They have a faster start-up speed compared to pilot-operated solenoid valves since they don't require a pressure difference. This makes it especially suitable for situations where fast opening and closing are necessary.
- Compact: Direct acting solenoid valves have the least moving mechanical parts of all solenoid valve types and are generally smaller; hence, they can be easily installed in tight spaces. They are commonly utilized in environments with small orifice diameters, typically less than 25 mm.
- Lower cost at small sizes: Direct acting solenoid valves have a simpler design and require fewer components, resulting in lower manufacturing costs. They are often more energy efficient, resulting in lower operating costs over time. However, for applications that involve high flow rates, the valve may need to employ larger solenoids, which could increase both the size and cost of the valve. Indirect acting solenoid valves are economical for higher flow rates. Consider the typical flow rate and system pressure to make a suitable choice between the solenoid valve types.
Disadvantages
- Small flow rates and low-pressure applications: Direct acting solenoid valves are not ideal for applications with high flow rates or pressures. These applications require a big orifice and a big solenoid, which increases the cost drastically. Therefore, direct operated solenoid valves are usually chosen for applications with small flow rates.
-
High power consumption: In a direct operated solenoid valve, the solenoid directly controls the movement of the valve stem. These valves require a continuous supply of electrical power to maintain the position of the valve. The power consumption is relatively high due to the solenoid's size and the magnetic field's strength required to move the valve plunger.
- However, once the plunger or armature is lifted and the valve is open, the electrical current can be reduced to a lower holding current, which is just enough to maintain the valve in the open position.
- Limited coil life: The coil can burn easily with a high-frequency power supply. This is because high-frequency electrical signals can generate excessive heat in the coil, causing it to overheat and burn out. The high-frequency electrical signals can also generate voltage spikes that can damage the insulation around the coil, leading to short circuits and other electrical problems.
Comparison with other solenoid valve types
Choosing the right solenoid valve type depends on the specific application requirements, such as the fluid type, flow rate, pressure, temperature, and environmental conditions. Table 1 summarizes the various factors to consider when selecting between solenoid valve types.
Table 1: Comparison between direct acting, indirect acting, and semi-direct acting solenoid valves
Solenoid valve type | Pressure tolerance | Pressure Difference | Speed | Power consumption | Coil life | Flow capacity | Purity of media | Cost |
Direct acting | Suitable for low-pressure, zero, and negative pressures | No required pressure difference | Fast | High
(5-20 W) |
Less | Low, typically a Kv < 0.865 | Can handle more fluid debris than indirect or semi-direct, but a strainer is still advised. | Low initial cost for low flow rate systems, cost increases as the flow rate increases |
Indirect acting | High-pressure applications. | Minimum pressure differential of 0.5 bar (7.3 psi) | Slow | Low (0.1-0.2W) | Medium | High, typically a Kv > 2.6 | Debris can clog the diaphragm. Using a strainer can increase back pressure and reduce efficiency. | Economical for large flow rate systems |
Semidirect acting | Suitable for low and high pressures | No pressure difference required | Medium | Low | High | High, typically a Kv > 2.6 | Debris can clog the diaphragm. Mounting a strainer before the solenoid valve can avoid clogging. | Economical for large flow rate systems |
Conclusion
Direct operating solenoid valves are suitable for applications where the valve needs to be responsive and provide quick opening and closing times. They are commonly used when there is limited space available for valve installation.
FAQ
What is the difference between direct acting and pilot solenoid valves?
Direct acting solenoid valves operate without needing an external pressure source, whereas pilot valves use the differential pressure of the fluid to control the valve. Direct acting valves are faster and more energy-efficient, while pilot valves can handle higher pressures and flow rates.
Read our humidifier, vacuum, and water solenoid valve articles for more details on the specific applications of solenoid valves.